This equipment has been tested and found to comply with the limits for a Class B digital device, pursuant to part 15 of FCC Rules. Tested To Comply With FCC Standards. Connect the Compaq Optical Mouse to any available USB port or hub connected to your computer. Para windows 7 busco el driver de tested to comply with fcc standard fcc registration Busco driver para optical mouse fcc standards for home or office use. 1 Comment DJI link. 1/6/2017 07:34:18 am. JE CHERCHE LOCICIEL DU CLAVIER FCC STANDARDS POUR MON PC Reply. Related Documents. Wireless Optical Mouse User Manual Feature 1. 2.4G frequency,digital cordless with distance up to 5-7meters 2.. Internal 65,000 group ID code,plug and play 3. 800/1200/1600DPI, high-precision and high- stabilization 4.. Self contained power switch, low power consumption,automatic sleeping function. As noted above, both the FCC and CE regulate aspects of mouse operations, so they also test and approve driver data. Byproducts/Waste Computer mice makers do not generate byproducts from mouse manufacture, but most offer a range of similar devices for different applications. These optical optical mouse with fcc standards are equipped with powerful sensors for better sensitivity and are made of sturdy materials to last for a long time. You can find optical mouse with fcc standards of different shapes, sizes, colors and designs at Alibaba.com and most of them come with a dependable standby time of no less than 60 days.
Background
Designers in the computer industry seek not only to 'build the better mousetrap' but to build the best mouse. The computer mouse is an accessory to the personal computer that has become an essential part of operation of the computer. The small device fits neatly in the curve of the user's hand and enables the user, through very limited movements of the hand and fingers to 'point and click' instructions to the computer. A rolling ball on the underside of the mouse gives directions on where to move to the cursor (pointer) on the monitor or screen, and one to three buttons (depending on design) allow the user to say yes by clicking the buttons on the right instruction for the computer's next operation.

History
Optical Mouse Tested To Comply With Fcc Standards Drivers License
Dr. Douglas Engelbart, a professor with the Stanford Research Institute in Menlo Park, California, developed the first device that came to be known as the mouse in 1964. At that time, the arrow keys on the keyboard were the only way of moving the cursor around on a computer screen, and the keys were inefficient and awkward. Dr. Engelbart made a small, brick-like mechanism with one button on top and two wheels on the underside. The two wheels detected horizontal and vertical movement, and the unit was somewhat difficult to maneuver. The unit was linked to the computer by a cable so the motion signals could be electrically transmitted to the computer for viewing on the monitor. One of Dr. Engelbart's co-workers thought the device with its long cable tail looked something like a mouse, and the name stuck.
Other scientists, notably those at the National Aeronautics and Space Administration (NASA), had also been seeking methods of moving cursors and pointing to objects on the computer screen. They tried steering wheels, knee switches, and light pens, but, in tests of these devices versus Engelbart's mouse, it was the mouse that roared. NASA's engineers were concerned, however, about the spacewalks the mouse would take from its work surface in the weightlessness of space.
By 1973, the wheels on the mouse's undercarriage had been replaced by a single, free-rolling ball; and two more buttons (for a total of three) had been added to the top. The creature was called both a mouse and a pointing device, and Xerox combined it with its Alto computer, one of the first personal computers. The Alto had a graphical user interface (GUI); that is, the user pointed to icons, or picture symbols, and lists of operations called menus and clicked on them to cause the computer to open a file, print, and perform other functions. This method of operating the computer was later adapted by Macintosh and Windows operating systems.
The development of the personal computer stimulated an explosion of applications for the device that was small enough to be used at a number of work stations. Engineers could develop computer-aided designs at their own desks, and the mouse was perfect for drawing and drafting. The mouse also began to generate offspring, collectively called input/output devices, such as the trackball, which is essentially a mouse lying on its back so the user can roll the ball instead of moving the entire unit over a surface. The military, air traffic controllers, and video game players now had a pet of their own. Mechanical sensors in both types of devices were replaced by optical-electronic sensor systems patented by Mouse Systems; these were more efficient and lower in cost. An optical mouse with no moving parts was developed for use on a special mouse pad with grid lines; light from inside the mouse illuminates the grid, a photodetector counts the number and orientation of the grid lines crossed, and the directional data are translated into cursor movements on screen.
The mouse began to multiply rapidly. Apple Computers introduced the Macintosh in 1984, and its operating system used a mouse. Other operating systems like Commodore's Amiga, Microsoft Windows, Visicorp's Vision, and many more incorporated graphical user interfaces and mice. Improvements were added to make sensors less prone to collecting dust, to make scrolling easier through an added wheel on the top, and to make the mouse cordless by using radio-frequency signals (borrowed from garage door openers) or infrared signals (adapted from television or remote controls).
Mouse Anatomy
Body
The mouse's 'skin' is the outer, hard plastic body that the user guides across a flat surface. It's 'tail' is the electrical cable leading out of one end of the mouse and finishing at the connection with the Central Processing Unit (CPU). At the tail end, one to three buttons are the external contacts to small electrical switches. The press of a button closes the switch with a click; electrically, the circuit is closed, and the computer has received a command.
On the underside of the mouse, a plastic hatch fits over a rubberized ball, exposing part of the ball. Inside, the ball is held in place by a support wheel and two shafts. As the ball rolls on a surface, one shaft turns with horizontal motion and the second responds to vertical motion. At one end of each of the two shafts, a spoked wheel also turns. As these spokes rotate, infrared light signals from a light-emitting diode (LED) flicker through the spokes and are intercepted by a light detector. The dark and light are translated by phototransistors into electrical pulses that go to the interface integrated circuit (IC) in the mouse. The pulses tell the IC that the ball has tracked left-right and up-down, and the IC instructs the cursor to move accordingly on the screen.

The interface integrated circuit is mounted on the printed circuit board (PCB) that is the skeleton to which all the internal workings of the mouse are attached. The integrated circuit, or computer chip, collects the information from the switches and the signals from the phototransistors and sends a data stream to the computer.
Brain
Each mouse design also has its own software called a driver. The driver is an external brain that enables the computer to understand the mouse's signals. The driver tells the computer how to interpret the mouse's IC data stream including speed, direction, and clicked commands. Some mouse drivers allow the user to assign specific actions to the buttons and to adjust the mouse's resolution (the relative distances the mouse and the cursor travel). Mice that are purchased as part of computer packages have the drivers built in or preprogrammed in the computers.
Raw Materials
The mouse's outer shell and most of its internal mechanical parts, including the shafts and spoked wheels, are made of acrylonitrile butadiene styrene (ABS) plastic that is injection-molded. The ball is metal that is coated in rubber; it is made by a specialty supplier. The electrical micro-switches (made of plastic and metal) are also off-the-shelf items supplied by subcontractors although mouse designers can specify force requirements for the switches to make them easier or firmer to click. Integrated circuits or chips can be standard items, although each manufacturer may have proprietary chips made for use in its complete line of products. Electrical cables and overmolds (end connectors) are also supplied by outside sources.
The printed circuit board (PCB) on which the electrical and mechanical components are mounted is custom-made to suit the mouse design. It is a flat, resin-coated sheet. Electrical resistors, capacitors, oscillators, integrated circuits (ICs), and other components are made of various types of metal, plastic, and silicon.
Design
Design of a new mouse begins with meetings among a product development manager, designer, marketing representative, and consulting ergonomist (a specialist in human motion and the effects various movements have on body parts). A list of human factors guidelines is developed specifying size range of hands, touch sensitivity, amount of work, support of the hand in a neutral position, the user's posture while operating the mouse, finger extension required to reach the buttons, use by both left- and right-handed individuals, no prolonged static electricity, and other comfort and safety requirements; these can differ widely, depending on whether the mouse is to be used in offices or with home computers, for example. A design brief for the proposed mouse is written to describe the purpose of the product and what it achieves; a look is also proposed in keeping with the anticipated market.
The design team returns to the table with foam models; scores of different shapes may be made for a single mouse design. User testing is done on these models; the engineers may do this preliminary testing themselves, or they may employ focus groups as typical users or observe one-on-one testing with sample users. When the selection of models is narrowed down, wooden models that are more refined and are painted are made of the winning designs. Input is gathered again on the feel, shape, and look of the models; the ergonomist also reviews the likely designs and confirms that the human factors guidelines have been achieved.
When the optimal model is chosen, the engineering team begins to design the internal components. A three-dimensional rendering is computer-generated, and the same data are used to machine-cut the shapes of the exterior shell with all its details. The mechanical and electronics engineers fit the printed circuit board (and its electronics) and the encoder mechanism (the ball, shafts, wheels and LED source and detector) inside the structure. The process of fitting the workings to the shell is iterative; changes are made, and the design-and-fit process is repeated until the mouse meets its design objectives and the design team is pleased with the results. Custom chips are designed, produced on a trial basis, and tested; custom electronics will help the design meet performance objectives and give it unique, competitive, and marketable characteristics.
The completed design diagrams are turned over to the project tooler who begins the process of modifying machines to produce the mouse. Tooling diagrams are generated for injection-molding the shell, for example. The size, shape, volume of the cavity, the number of gates through which the plastic will be injected into the mold, and the flow of the plastic through the mold are all diagramed and studied. After the final tooling plan is reviewed, tools are cut using the computer-generated data. Sample plastic shells are made as 'try shots' to examine actual flow lines and confirm that voids aren't induced. Changes are made until the process is perfect. Texture is added to the external appearance of the shell by acid etching or by sand blasting.
In the meantime, the engineering team has set up the assembly line for the new mouse design and conducted trial assemblies. When the design details are finalized, tools have been produced, and test results have met the design team's objectives and standards, the mouse is ready for mass production.
The Manufacturing
Process
To make the computer mouse, several manufacturing processes are performed simultaneously to make different pieces of the unit. These processes are described in the first three steps below. The pieces are then brought together for final assembly, as described in steps 4 through 7.
- In one of the sets of manufacturing and assembling steps, the printed circuit board (PCB) is cut and prepared. It is a flat, resin-coated sheet that can be of surface-mount design or through-hole design. The surface-mount version is assembled almost entirely by machine. A computer-controlled automatic sequencer places the electrical components in the proper order onto the board in a prescribed pattern.
For through-hole PCB assembly, attachment wires of the electronic components are inserted in holes in the PCB. Each assembly line worker has a drawing for part of the board and specific units to add. After all the components are mounted on the board, the bottom surface of the board is passed through molten lead solder in a wave soldering machine. This machine washes the board with flux to remove contaminants, then heats the board and the components it carries by infrared heat to lessen the possibility of thermal shock. As the underside of the board flows over the completely smooth, thin liquid sheet of molten solder, the solder moves up each wire by capillary action, seals the perforations, and fixes the components in place. The soldered boards are cooled. The PCB is visually inspected at this stage, and imperfect boards are rejected before the encoder mechanism is attached.
- The encoder mechanism (including the rubber-covered ball, the support wheel, both spoked wheels and their axles, the LED, and its detector) is assembled as a separate unit. The plastic parts were also manufactured by injection-molding in accordance with proprietary specifications and trimmed of scrap plastic. After the mechanism is assembled, the unit is fastened to the PCB using either clips or screws. The board is now completely assembled and is subjected to an electronics quality control test.
- The mouse's tail—its electrical cable—has also been manufactured using a set of wires, shielding, and the rubber cover. The cable has two additional pieces of molded rubber called overmolds. These are strain relief devices that prevent the cable from detaching from the mouse or its connector plug if the cable is tugged. Mouse makers typically design their own shapes for overmolds. The near-mouse overmold is hooked to the housing, and, at the opposite end of the tail, the connector is soldered to the wires and the connector overmold is popped into place.
- The pieces of the outer shell are visually inspected after molding, trimming, and surface (finish) treatment and prior to assembly. The outer shell is assembled in four steps. The completed PCB and encoder assembly is inserted into the bottom of the shell. The buttons are snapped into the top part of the housing, the cable is attached, and the top and bottom are screwed together using automated screwdrivers.
- The final electronics and performance quality check is performed when assembly is essentially complete. Rubber or neoprene feet with adhesive sheeting pre-applied to one side are added to the underside of the mouse.
- While the tooling designs and physical assembly described above have been in progress, a programming team has been developing, testing, and reproducing the mouse driver firmware. The firmware so-called because it lies in the realm between software and hardware consists of a combination of codes in the integrated circuit and the translation of the mouse's directional movements and micro-switch signals that the receiving computer needs to understand when the mouse is attached. When the driver has been developed, the manufacturer's own testers run it through rigorous trials, and both the Federal Communications Commission (FCC) and the European Commission (CE—an organization that governs radio emissions and electrostatic discharge) also approve the electronics. Approved driver data is encoded and mass-produced on diskettes.
- The FCC requires that signaling or communications devices including the mouse bear labels identifying the company and certain product specifications. The labels are preprinted on durable paper with strong adhesive so they cannot easily be removed. A label is pasted on the mouse bottom, and the mouse is bagged in plastic. The device, its driver diskette, and an instruction booklet with registration and warrantee information are boxed and prepared for shipment and sale.
Quality Control
Use of computer-generated designs builds quality and time savings into the product. Data can be stored and modified quickly, so experiments with shapes, component layouts, and overall look can be attempted and iterative adjustments can be made. Computer-aided design data also speeds review of
At least three quality control steps are performed during assembly. An electronics check is carried out on the PCB after its components are attached (and soldered into place if through-hole assembly methods are used) and before any of the plastic mechanism is attached. The plastic parts (the encoder mechanism and the outer shell) are visually inspected when they are complete but before they are connected to the board and electronics; this prevents disassembly or wasting electronics due to a defective shell, for example. Finally, the completely assembled device is subjected to another electronics and performance check; 100% of the mice manufactured by Kensington Technology Group are plugged into operating computers and tested before they are packaged. As noted above, both the FCC and CE regulate aspects of mouse operations, so they also test and approve driver data.
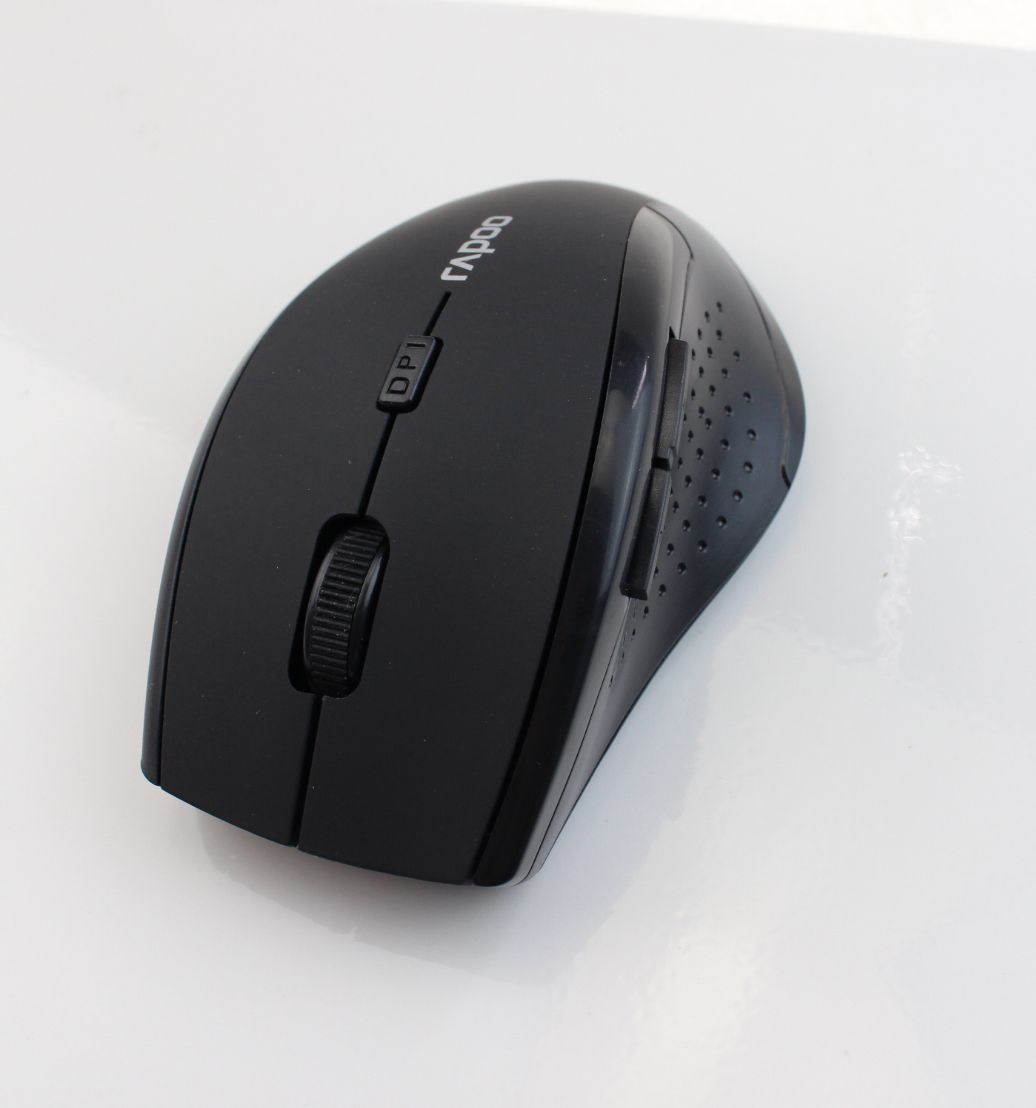
Byproducts/Waste
Computer mice makers do not generate byproducts from mouse manufacture, but most offer a range of similar devices for different applications. Compatible or interchangeable parts are incorporated in new designs or multiple designs whenever possible to avoid design, tooling, and assembly modification costs.
Waste is minimal. The mouse's ABS plastic skin is highly recyclable and can be ground, molded, and reground many times. Other plastic and metal scrap is produced in minute quantities and can be recycled or disposed.
The Future
Devices that are modifications of mice are currently on the market. The Internet mouse inserts a scrolling wheel between the two buttons to make scrolling of web pages easier; a still more sophisticated version adds buttons that can be programmed by the user to perform Internet functions, like moving back or forward, returning to the home page, or starting a new search. One mouse version has returned to the floor where two foot pads or pedals replace the ball and buttons; one pedal is pushed to relocate the cursor and the second clicks. Cordless mice that communicate with radio signals are available, and the mouse has been disposed of altogether by the touchpad. The user runs a finger across the touchpad to reposition the cursor, and web pages can be scrolled and advanced by other, specific moves. Many of these adaptations are designed to eliminate repetitive stress ailments and save forearm strain.
The mouse's inventor, Dr. Engelbart, never believed the mouse would reach thirty-something or retain its nontechnical name. In fact, both the mouse and its trackball offspring are increasingly popular as shapes become more comfortable, less cleaning and maintenance are required, and reliability and longevity improve. Future developments in mice will follow the evolution of the Internet and include more options for programmability, such as switching hands to double the number of available functions. The mouse may become extinct someday, and the most likely candidate to replace it is a device that tracks the eye movement of the computer user and follows it with appropriate cursor motions and function signals.
Where to Learn More
Books
Ed., Time-Life Books. Input/Output: Understanding Computers. Alexandria, VA: Time-Life Books, 1990.
Periodicals
Alexander, Howard. 'Behold the Lowly Mouse: Clever Technology Close at Hand.' New York Times (October 1, 1998): D9.
'The Mouse.' Newsweek (Winter 1997): 30.
Randall, Neil. PC Magazine (January 5, 1997): 217.
Terrell, Kenneth. 'A new clique of mice: designers turn the computer mouse on its head; some cut its tail.' U.S. News & World Report (March 23, 1998): 60+.
Other
Kensington Technology Group. http://www.kensington.com/ (June 7, 1999).
Logitech. http://www.logitech.com/ (June 7, 1999).
Microsoft Corporation. http://www.microsoft.com/ (June 7, 1999).
The FCC regulates radio frequency (RF) devices contained in electronic-electrical products that are capable of emitting radio frequency energy by radiation, conduction, or other means. These products have the potential to cause interference to radio services operating in the radio frequency range of 9 kHz to 3000 GHz.
Almost all electronic-electrical products (devices) are capable of emitting radio frequency energy. Most, but not all, of these products must be tested to demonstrate compliance to the FCC rules for each type of electrical function that is contained in the product. As a general rule, products that, by design, contain circuitry that operates in the radio frequency spectrum need to demonstrate compliance using the applicable FCC equipment authorization procedure (i.e., Supplier's Declaration of Conformity (SDoC) or Certification) as specified in the FCC rules depending on the type of device. A product may contain one device or multiple devices with the possibility that one or both of the equipment authorization procedures apply. An RF device must be approved using the appropriate equipment authorization procedure before it can be marketed, imported, or used in the United States.
The following discussions and descriptions are provided to help identify whether a product is regulated by the FCC and whether it requires approval. The more difficult issue, but not covered in this document, is how to categorize an individual RF device (or multiple components or devices within an end product) to determine the specific FCC rule part(s) that apply, and the specific equipment authorization procedure or procedures that need to be used for FCC compliance purposes. This determination requires technical understanding of the product, as well as knowledge of the FCC rules.
2.4 Ghz Wireless Optical Mouse Tested To Comply With Fcc Standards Driver
Some basic guidance on how to obtain an equipment authorization is provided at the Equipment Authorization Page.
INCIDENTAL RADIATORS (Part 15, Subpart A)
An incidental radiator (defined in Section 15.3 (n)) is an electrical device that is not designed to intentionally use, intentionally generate or intentionally emit radio frequency energy over 9 kHz. However, an incidental radiator may produce byproducts of radio emissions above 9 kHz and cause radio interference. A product that is classified as an incidental radiator device is not required to obtain an equipment authorization. Nonetheless, incidental radiator are regulated under the general operating conditions of Section 15.5 and if there is harmful interference the user must stop operation and remedy the interference. Manufacturers and importers should use good engineering judgment before they market and sell these products, to minimize possible interference (Section 15.13).
Examples of products that are classified as incidental radiators include: AC and DC motors, mechanical light switches, basic electrical power tools (that do not contain digital logic).
UNINTENTIONAL RADIATORS (Part 15, Subparts B and G)
An unintentional radiator (defined in Section 15.3 (z)) is a device that by design uses digital logic, or electrical signals operating at radio frequencies for use within the product, or sends radio frequency signals by conduction to associated equipment via connecting wiring, but is not intended to emit RF energy wirelessly by radiation or induction.
Today the majority of electronic-electrical products use digital logic, operating between 9 kHz to 3000 GHz and are regulated under 47 CFR Part 15 Subpart B.
Optical Mouse Tested To Comply With Fcc Standards Drivers
Examples include: coffee pots, wrist watches, cash registers, personal computers, printers, telephones, garage door receivers, wireless temperature probe receiver, RF universal remote control and thousands of other types of common electronic-electrical equipment that rely on digital technology. This also includes many traditional products that were once classified as incidental radiators – like motors and basic electrical power tools that now use digital logic.
Products that only contain digital logic may also be specifically exempted from an equipment authorization under Section 15.103.
INTENTIONAL RADIATORS (Part 15, Subparts C through F and H)
An intentional radiator (defined in Section 15.3 (o)) is a device that intentionally generates and emits radio frequency energy by radiation or induction that may be operated without an individual license.
Examples include: wireless garage door openers, wireless microphones, RF universal remote control devices, cordless telephones, wireless alarm systems, Wi-Fi transmitters, and Bluetooth radio devices.
INDUSTRIAL, SCIENTIFIC, AND MEDICAL EQUIPMENT (Part 18)
When electronic-electrical products are used for providing RF energy for other than telecommunications applications, such as for the production of physical, biological, or chemical effects, such as heating, ionization of gases, mechanical vibrations, and acceleration of charged particles, these devices fall under the FCC rules 47 CFR Part 18.
Examples include: fluorescent lighting, halogen ballasts, arc welders, microwave ovens, and medical diathermy machines.
Note: A general consumer medical device does not typically come under this classification; rather Part 18 applies for medical equipment only when it is designed to generate and use RF energy locally for medical or therapeutic purposes.
EQUIPMENT OPERATING IN LICENSED RADIO SERVICES
Products that use licensed radio spectrum, from fixed microwave links to cellular telephones to mobile broadband services, are considered RF devices and are subject to equipment authorization.
Examples of licensed radio equipment subject to Certification include: low power TV transmitters, cell phones/smart phones, base stations, licensed point-to-point microwave radios, private land mobile transmitters, aviation and marine radios.
For more information on licensed radio services:
Radio spectrum allocation, regulatory responsibility for the radio spectrum is divided between the Federal Communications Commission (FCC) (non-Government uses) and the National Telecommunications and Information Administration (NTIA) (Government agencies usage). At present only frequency bands between 9 kHz and 275 GHz have been allocated (i.e., designated for use by one or more terrestrial or space radiocommunication services, or for the radio astronomy service under specified conditions). OET maintains the FCC's Table of Frequency Allocations, which is a compilation of allocations. The FCC’s Table of Frequency Allocations is codified at Section 2.106 of the Commission's Rules. For a more detailed description go to the Table of Frequency Allocations Chart.